

轴承是核心基础零部件,轴承工业是国家基础性战略性产业,对国民经济发展和国防建设起着重要的支撑作用,建国以来,特别是改革开放以来的持续、快速发展,我国轴承工业已形成独立完整的工业体系,我国已成为轴承销售额和产量居世界第三位的轴承生产大国。并向世界轴承强国迈进。制别是“十三五”时期,我国轴承行业的众多企业,奋力拼搏,攻坚克难,逆势而上,保持全行业平稳较快发展,为建成世界轴承强国打下了良好基础。2022年统计,全行业规模以上企业1300多家,主营业务收入2232亿元,轴承产量212亿套。2022年我国共累计出口创汇72.55亿美元,进口轴承用汇45.64亿美元,进口轴承27.21亿套。我国已是世界轴承生产大国,但还不是世界轴承强国,产业结构、研发能力、技术水平、产品质量、效率效益都与国际先进水平有较大差距。国内现有近10000家轴承及轴承产品相关企业,其中中低端产品占比>80% ,全球高端轴承市场容量中,中国企业仅占有5% 。一、滚子是轴承产业链的关键环节
滚子轴承是滚动轴承产品的重要类型,滚子轴承包括圆柱滚子轴承、圆柱滚子轴承、调心滚子轴承。尺寸范围以大型、特大型、重载轴承居多,主要应用在工程机械、冶金矿山、汽车、高铁、风电等主机行业。滚子是滚子轴承的关键零件,其精度、性能、寿命和可靠性对成套轴承精度、性能、寿命和可靠性的具有重要影响。因此滚子制造是轴承产业链的关键环节。由于受技术水平和装备能力的限制,轴承行业目前尚不能批量生产0级、i级精密滚子,无论从高端轴承的自主配套,还是从轴承产业链的安全可控的角度考虑,精密滚子的制造都与滚子轴承的发展要求不相适应,已成为配套重大装备高端轴承的瓶颈。从统计报表数字来看:2022年1-12月全国轴承进口量为272077.56万套,进口用汇:368626.86万美元,其中:圆柱滚子轴承、圆锥滚子轴承进口数量:14414.14万套;占全国轴承进口量的5.3%;圆柱滚子轴承、圆锥滚子轴承进口用汇:121927.22万美元;占全国轴承进口用汇的33.07%;可见进口轴承圆柱、圆锥滚子轴承用汇占比较高,说明滚子轴承进口的附加值较高,属于高端精密轴承。也就是说,我国高端精密滚子轴承还有相当部分需要进口,如风电主轴轴承。“十三五”以来轴承行业对滚子的研发与制造高度重视,特别是“十四五”规划启动一、二年许多企业通过引进消化先进的滚子磨超线,并积极为高端主机配套取得了一定的进展。轴承行业的科研单位和高等院校,面向企业,聚焦难点,在圆锥滚子凸度超精加工与装备领域不断探索,完成了国家自然科学基金面上项目;“圆锥滚子凸度贯穿式超精研修形机理与规律”课题研究,取得科研成果,“圆锥滚子凸度贯穿式超精研关键技术”获得“中国机械工业科学技术奖”二等奖,并相应取得国家发明专利。装备制造企业从满足高端轴承需求出发,从装备的研发入手,组建滚子全自动生产线,逐步形成从加工到包装的全过程自动化操作;滚子生产龙头企业自筹资金引进国外的先进生产线,坚持引进与消化相结合,结合企业实际,探索适合自己特点的滚子性能提升之路。1、江苏力星钢球股份有限公司最新引进意大利、德国滚子生产线,公司目前具备12条生产线。生产φ6mm—φ80mm圆锥滚子和φ20mm—φ80mm圆柱滚子。月产能达到1050吨/月,年产能12680吨/年。目前φ25mm以下的圆锥滚子均具备批量i、ⅱ级滚子的生产能力,ⅰ、ⅱ滚子的生产比例根据客户的图纸要求执行。目前ⅰ级滚子占比25%。圆柱滚子目前所生产的产品基本都是风电产品,基本都为g1a级,占比80%,而供应部分铁路圆柱滚子基本都是g1级,占比20%,生产的以圆锥滚子主要应用于风电、重卡、轨道交通、商务车等。2、浙江五洲新春集团有限公司从2019年开始生产风电变桨轴承用圆柱滚子和部分主轴用圆锥滚子,其主要生产设备是国产的,但在技术上优化表面轮廓、热处理工艺(新上了3条盐浴炉专线),风电主轴轴承圆锥滚子约60000粒/月,产品大部分达到或接近ⅰ级精度,变桨圆柱滚子约150万粒/月,基本上满足了轴承成品的质量要求,随着风电轴承量的增加,也在不断技改建线扩大产能。3、山东东阿钢球集团有限公司从2009年也开始生产圆柱和圆锥滚子,圆柱滚子可生产精度0;ⅰ、ⅱ级滚子。圆柱滚子以ⅱ级以上为主。圆锥滚子可生产精度ⅱ、ⅲ 级滚子,个别项目可达ⅰ级精度。ⅲ级滚子占比60%左右,其余为ⅱ级、ⅰ级,现引进的最先进英国泰勒圆度仪,并按舍弗勒的圆度、波纹度判定标准控制,外观普遍采用智能自动化检测装备,引入ai视觉技术,实现了滚子表面缺陷高效稳定准确检测。为配套高端装备和滚子零件出口打下了良好的基础。4、瓦房店威远滚动体制造有限公司主要生产中大型圆柱、球面、圆锥滚子,为轧机、矿山冶金及风电轴承配套,并部分出口欧美市场,年生产能力约1000万粒,其中圆柱滚子和球面滚子占85%以上。5、宁波海亚特滚子有限公司目前圆柱滚子年产量1.2亿粒、圆锥滚子9.36亿(其中出口比例约为35%),有圆柱滚子生产线4条,2022年产量0.73亿粒;圆锥滚子生产线共33条,2022年产量5.72亿粒,其中:中型圆锥滚子15条,年产量1.14亿粒,小型圆锥滚子18条,年产量4.58亿粒;全年产量约6.4亿粒,国内市场占有率为全国第一,目前生产的大多数圆柱、圆锥滚子为ⅱ级滚子技术要求。大部分产品的精度与ⅱ级滚子的要求相近。还有新昌诚本、宁波荣成华盛、洛阳鸿盛等专业滚子生产厂都有生产,除专业生产厂家外,轴承主要生产厂家如:瓦轴、洛轴、人本、天马、甘肃海林中科、襄轴、西北轴、大冶轴及洛阳新强联等自己也生产圆柱和圆锥滚子,基本上能满足目前的市场需求,当然这些轴承生产厂家也要从一些主要滚动体生产厂家购买高精度滚子。从以上情况看,目前我国轴承行业圆柱和圆锥滚子生产情况:主要以ⅱ级、ⅲ级滚子为主约占80%, i级滚子占比约5%左右,)0级滚子占比约5%以下)。国内滚子制造装备与国际先进水平有一定差距,但近几年国内滚子装备厂家在学习国外先进设备的基础上进行的设备开发,还是取得了一定的成果,例如滚子高速冷镦机,滚子数控无心磨床,滚子数控球基面磨床,滚子超精机等设备的成功开发,提升了国内滚子装备的技术水平。国内滚子检测装备,特别是视觉检测装备,已经与国外设备相当或超过国外设备,例如滚子在线外观检测,国内生产的设备在市场占有率上已经远超欧美和日本。但是,与主机行业高端轴承的配套需求相比,滚子现阶段的性能指标仍然存在一定的差距。这一瓶颈的有效突破,需要行业上下有识之士的共同努力,需要轴承零部件企业的技术进步和转型升级,需要轴承生产企业和滚子制造企业的密切配合。突破这一瓶颈,已成为我国轴承行业推进转型升级,由大到强的重要关键环节。中华人民共和国国家标准gb/t25767-2010《滚动轴承圆锥滚子》、gb/t4661-2015《滚动轴承圆柱滚子》明确规定了圆锥滚子和圆柱滚子的各参数定义和各项精度指标。圆柱滚子直径公差和轴向跳动(gb/t25767—2010)单位为微米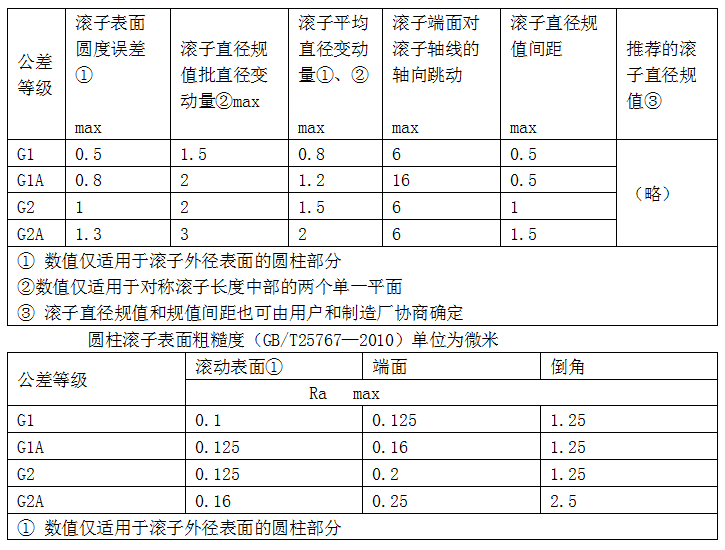
圆锥滚子表面粗糙度(gb/t25767—2010) 单位为微米
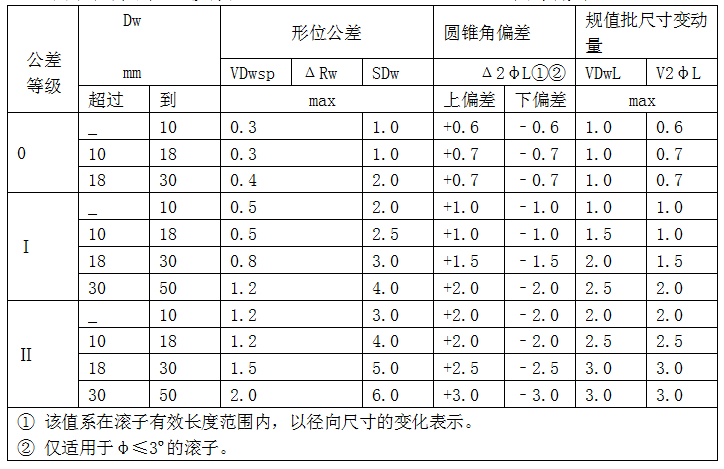
但是目前行业的制造水平受到各种条件的制约,我国轴承企业只能批量生产g2级圆柱滚子和ⅲ级圆锥滚子,满足不了高端轴承的配套要求。从开发高端轴承的需要出发,轴承滚子技术质量水平必须达到:能够批量生产g1级圆柱滚子、ⅰ级圆锥滚子和ⅱ级球面滚子。轴承钢材料的质量对轴承产品的加工质量、使用寿命和可靠性的优劣起着至关重要的作用。随着先进工艺及设备的引进,我国轴承钢的冶炼水平、冶金质量上了一个台阶,在一些技术和质量指标方面达到或接近国外的先进水平,但整体质量水平与发达国家的质量水平仍有着较大的差距,表现为:现行的轴承钢材料标准中,对碳化物颗粒大小及分布状态的质量控制情况无内容,使得碳化物颗粒大小及分布状态国外存在有较大的差距,这也是我国轴承产品使用寿命和可靠性低于国外同类产品的一个主要原因。另外,在《高碳铬轴承钢》(gb/t18254)中关于非金属夹杂物检验评级方法目前对于低氧量、高纯洁度轴承钢具有一定的局限性,已不能准确地评价轴承钢中的非金属夹杂物,国外已采用其它的检验方法进行评级,所以只有在以上方面有所突破,我国轴承钢的质量和轴承产品的质量才能有所提高。直径大于60mm高碳铬轴承钢滚子原材料在gb/t18254中没有网状碳化物要求,导致热处理组织不好控制。如我国生产轴承钢中的氧含量已接近国外生产轴承钢先进国家的水平,但轴承钢中非金属夹杂物的颗粒大小、分布状态很不均匀,有的视场一颗非金属夹杂物都没有,有的视场则大量出现,点状不变形夹杂不仅出现的概率频繁,而且颗粒尺寸较大。原材料的可塑性、化学元素成分的稳定性、纯净度以及颗粒结构均是目前制约我们滚子行业发展的瓶颈环节,同样也制约轴承寿命。3、我国轴承滚子技术水平与国际先进水平的差距突出表现在轴承滚子工艺装备。目前国外加工基本为连线布置,而国内轴承滚子的加工大多采用单机、多工序、多工步加工,有些环节加工机床精度差、稳定性差,所加工的轴承滚子存在尺寸散差大,几何精度不统一、不稳定等问题,导致生产出来的轴承状态不一致、寿命不稳定。其中滚子成型,国内大型轴承公司同国外一样,采用冷镦成型,但使用的冷镦设备要较国外(多工位冷镦机)落后,适用滚子尺寸也要小很多。随着基础制造业水平的逐步提升,国内滚子加工设备的制造和模仿能力有所提升,与国外对比处于不同级水平。机床设计原理以及加工用材的材质、加工技术,目前仍制约着设备性能的发挥。同时修磨工装的辅助加工设备同样也是限制机床性能发挥的主要因素之一。国内设备厂家更多关注的还是机床如何实现磨削的功能,对机床使用寿命的防护仍未提上设计的日程,国内机床目前仍未实现模块化装配,无法保障设备精度。由于对引进设备的消化吸收再创新没有取得突破性发展,致使不能稳定批量生产为高端轴承配套的0级、ⅰ级高精度滚子。冷镦-软窜-软磨外径-软磨端面-热处理-抛丸-光饰——转硬磨车间连线生产-粗磨外径-双端面1-细磨外径-双端面2-光饰/端面精研-终磨1-终磨2--超精-清洗-光电外观检验-分选-涂油-包装。2)主要设备为:冷镦机、光饰机、外径磨床、端面精研机、超精机。冷镦-软窜-软磨外径-软磨端面-热处理-抛丸-光饰——转硬磨车间连线生产-磨外径(粗磨、细磨)-磨球基面(粗磨、细磨)-终磨外径(1~3遍)-超精外径-清洗-外观检验(光电、人工)-涂油-码料-包装。4)主要设备为:冷镦机、外径磨床、球基面磨床,其中球基面磨削形式很多,主要是圆盘式磨削和范成法磨削,范成法磨削相对精度稍高一些,但效率较低,适用于尺寸较大的滚子,当然还有其他磨削方式。滚子外径超精机、清洗设备、光电外观检验、涂油包装等。沿用多年的仿苏滚子冷镦机十分落后,必须彻底淘汰。引进的滚子多工位冷镦机加工精度高,加工效率高,但价格昂贵,一般企业无力购置。近年来,国内一些设备制造企业在对引进的滚子多工位冷镦机的消化吸收再创新上做了很大努力,取得一定进展,但与国际先进水平还有很大差距。对引进的高精度数控滚子外圆磨床的技术特点,如伺服数控、砂轮和导轮的刚性支承、大直径和大宽度的砂轮、大直径和大宽度的导轮、组合砂轮的应用、砂轮双伺服插补修整和自动补偿、导轮在机自修整等技术特点进入深入研究,消化吸收再创新,研发应用达到国际先进水平的高精度数控滚子外圆磨床。对引进的高精度滚子外圆数控超精机的技术特点,如大直径大宽度的超精辊、大往复小振荡的振荡器的应用进行深入研究,消化吸收再创新,研发应用达到国际先进水平的高精度滚子外圆数控超精机。研发应用专用超精导辊磨床,导辊磨加工后形成对滚子支承的特殊型面,使滚子通过超精,达到设计要求的对数曲线凸度或修型。目前,从多个国家引进的多种型式的滚子数控球基面磨床,有的型式加工精度高,但加工效率低,有的型式加工效率高,但加工精度低。应对引进的各种型式的球基面磨床进行深入研究,博采众长,把着力点放在自主创新上,研制适合我国国情的,加工精度和加工效率高,性价比好的滚子数控球基面磨床。目前国内的检测仪器相对落后,国外检验设备与时俱进,更多依据计算机控制判断,而国内成熟的,基本的在线检测技术和设备没有普遍采用,很多还是靠人工外观检验,影响生产效率和产品质量。目前国内多数专业滚子生产厂或轴承厂经近几年的设备改造上了很多条滚子磨超自动线,但多数由于设备本身精度问题,致使连线过长,占地面积较大,影响滚子生产效率和产品质量。研发应用滚子滚动表面、球基面、端面凹穴、倒角的主要技术指标全项检测的专用数字化仪器和设备。但是,设备的性能稳定性和精度保持性、联线技术和系统集成能力与国际先进水平有较大差距,特别是滚子加工关键设备的引进消化吸收再创新没有取得突破性进展,以至不能稳定批量生产为高端轴承配套的i级圆柱滚子、i级圆锥滚子。滚子轴承是滚动轴承中重要的结构类型,是高端轴承重要的组成部分之一。在大型机械、重载领域具有不可替代的作用。特别是在高速铁路、盾构机械、风力发电行业,滚子轴承自主化的要求越来越迫切。轴承滚子的发展水平不仅关系到轴承行业产品的高端突破,而且关系到主机产业链的安全可控等重大问题。按全国轴承行业“十四五”发展规划 2025年发展目标:轴承产量250亿套,销售收入2500(2237~2583)亿元 ,预计2025年全球轴承产品总需求达到1500亿美元,其中滚子总需求达到150亿美元。据2021年轴承行业统计111家企业,2021年滚子轴承(这里指圆柱、圆锥)产值占整个轴承产值的19.27%,尤其是为重点主机配套的高端滚子轴承轴承,其相应的公差等级要求亦为i级甚至o级公差。这里列举几个重点领域在仅近一、二年滚子轴承市场的情况:盾构机轴承要求较高。刀盘是盾构机的关键部件,在隧道掘进过程中发挥着重要作用。刀盘系统中的主轴承是传递掘进动力和运动的核心零件,在工作中承受着巨大的轴向力、倾覆力矩和一定的径向力,其性能、寿命和可靠性直接影响盾构机的施工进度、安全和掘进里程。盾构机主轴滚子年需求量约1.4亿元。国内地铁用盾构机需求量约2000台,年需求量约400台(其中国产约300台)。另有国内在役的盾构机约1800余台,在役盾构机主轴承超过设计寿命后均需要维修和更换。盾构机主轴价值两大,一套价格约300万元。预计盾构机主轴承年需求量达400套、约12亿元,滚子占比10-15%,以12%计,盾构机主轴滚子年市场需求量约1.4亿元。目前风电主轴轴承国产化率33.0%,基本上都是3.0兆瓦及以下,轴承行业刚进入这一领域,需要加大技术攻关和市场开拓的力度。齿轮箱轴承国产化率仅为0.58%,发电机轴承国产化率仅为0.2%,应该说,这二个领域的门槛,轴承行业还没有真正跨进去,而风电主轴轴承和齿轮箱轴承多为圆柱滚子和圆锥滚子轴承,其精度要求为p5级以上,现大部分还依赖进口,其中滚动体的精度及母线修形形状也是影响轴承精度的主要原因之一,可喜的是,大功率风电主轴轴承的研发已有了进展,风电滚子的技术优化主要依赖第三梯队。滚子市场竞争格局分四大梯队,第一梯度为外资品牌,技术力强,可以自制但成本较高,部分企业开始国内采购;第二梯度为国内头部轴承企业,可以生产滚子匹配公司主轴、齿轮箱等产品,但是滚子成本占轴承总成本的10-15%,而滚子研发投入大,设备与轴承套圈等设备不匹配,因此国内头部轴承厂商投资效率不高,投资积极性低;第三梯队为专业滚子生产厂,滚子研发投入最有效率。第四梯队为普通工业轴承滚子厂,规模小,数量多,国内超1050家,工艺技术无法达到一、二级滚子的技术要求。国产滚子部分技术达国际领先水平,加速滚子大兆瓦进口替代进程。五洲新春、力星可供货4mw以上风电滚子,加速推动大兆瓦国产化进程。滚子与套圈尺寸相差较大,国内轴承厂商改进滚子工艺的积极性不高。风电轴承滚子尺寸在15-750px,风电轴承套圈直径超1m,而这尺寸差距显著,在热处理、磨加工环节上设备不可共用,且风电滚子轮廓线加工、 磨加工工艺要求高,需要企业投入大量研发精力,未来国内风电滚子市场预计主要被专业滚子厂垄断。高铁动车组轴承性能要求高。目前国内高铁轴承多为国外进口。高铁crh1和高铁crh5使用skf轴承,高铁crh2使用ntn和nsk轴承, 高铁crh3使用fag轴承。高铁轴承主要是在高速重载运动状态下工作,服役条件极为恶劣,对轴承要求高。以crh5为例,平均值估算每套轴承载荷约为68.7kn,最大滚动体载荷约为7.6kn,内圈滚道与滚子 的接触应力约为810mpa,轴承转速约为1730r/min。高铁轴承为存量替换市场。对于最高运营速度不大于200km/h 的轴承,质保期为90万公里(或4年),最高运营速度大于200km/h的轴承,有定期检修,240万公里后必须报废。高铁轴承滚子有近7亿市场空间。4、其它滚子类高端轴承如:城市轨道交通地铁轴承、机床轴轴承、重卡轮毂轴承等亦有较大的市场。目前我国轴承滚子的技术水平与国际先进水平的差距还是比较大,在轴承钢、加工装备、生产工艺、检测仪器及管理等方面都有一定的差距。为了尽快减少差距,我国必须在这几个方面加大科研投资力度,使我国轴承产业尽快实现从量变到质变的升级,解决我国高端轴承长期依赖进口的问题。按照轴承行业“十四五”专题规划,发展目标为:“坚持问题导向,以技术创新为手段,优化工艺路线,从提高产品质量入手,补齐发展短板,通过技术、人才、管理等措施的综合运用,使轴承滚子的产品性能稳步提升,满足轴承行业高质量发展的需要,满足高端轴承配套重大装备的战略需求”。全行业要深刻认识轴承滚子在主机产业链中的重要性,把提高轴承滚子的制造水平,放到产业基础高级化、产业链现代化的大背景下去审视,放到产业链安全可控的重要地位中去认识。国家要进一步加大对包括轴承滚子在内的机械基础零部件的关注程度和支持力度。特别是对于自主创新,替代进口的研发与生产应给与必要的政策支持和资金扶持。在国家重大科研项目中给以优先立项,组织力量重点突破。轴承滚子技术指标多,产品精度高,生产具有专业性,既具有技术密集型的特点,也具有劳动密集型的特色。鼓励企业根据自身的特点,完善制造工艺,优化制造模式。通过3—5年的努力,行业内要形成2—3家在轴承行业有一定影响力,产品技术指标达到国际先进水平的轴承滚子龙头企业。同时也要鼓励轴承行业的排头兵企业,自己建立轴承滚子分厂,建立自身的产品产业链条,满足自身产品的配套需求。通过实施两条腿走路的方案,实现优势互补,共同促进,实现轴承滚子制造的可持续发展。创新是行业发展的核心驱动力。各部门要鼓励大专院校和科研单位加大对轴承滚子基础应用的研究,用创新的思维解决企业技术创新中的难点问题。积极支持轴承滚子制造企业创建国家级的企业技术中心,建立企业技术创新平台,不断培育新动能。围绕产业链部署创新链,围绕创新链布局产业链。实现产业链与创新链的有效融合。市场的竞争归根结底是人才的竞争,人才的竞争的核心是教育。要通过各种形式加强对轴承滚子专业人才的培养和培训,采用请进来,走出去的方法,让企业与高等院校专家进行交流,通过建立院士工作站、博士后工作站的方式,加强一线技术人员与专家学者的交流与互动,让专家在一线发现课题,为一线解决难题。通过中国轴承工业协会人力资源委员会依托河南科技大学开设“轴承滚子制造技术与应用专班”的方式,为轴承滚子技术人才的培养进行探索,其目的是形成理论联系实际的轴承行业滚动体人才梯队。瞄准国外高端轴承滚子的技术指标和使用寿命,从产品精度和使用性能两方面进行对照,抓住关键环节,力争取得突破;把国产机床和进口机床加工的轴承滚子进行对比,找出弱项,发现问题,有的放矢制定凯发k8娱乐的解决方案。把gb/t25767-2010《滚动轴承圆锥滚子》、gb/t4661-2015《滚动轴承圆柱滚子》国家标准,作为对生产企业的基本要求,完善工艺规程和检测手段,实现轴承滚子制造的转型升级。工欲善其事,必先利其器。长期以来,国产滚子专用装备与国际先进水平有很大差距,制约了滚子技术质量水平的提升,滚子产品升级,装备必须先行。冷镦作为轴承滚子制造的前道工序,对滚子的加工效率和质量水平有重要的影响。争取组织相关单位和部门对现存的单工位、双工位、多工位冷镦工艺和设备的进行分析和比较,综合先进性、实用性、经济型等多种因素,在冷镦技术应用上,逐步做到淘汰单工位、普及双工位、提倡多工位。以优化冷镦工艺为切入点,研制适合中国国情、加工精度和加工效率达国际先进水平,而造价和后续使用费用较低的滚子多工位冷镦机,投放市场,形成一套以工艺装备为依托的、先进、实用、可靠的轴承滚子冷镦技术,促使我国轴承行业滚子成形工艺及装备水平达到国际先进水平。近几年国内相继引进了国外高精度数控磨床用以加工滚子。一些设备厂家在对这些引进设备的消化吸收再创新上进行了初步尝试。在此基础上,国内设备厂家要进一步对滚子磨加工工艺和装备进行深入的研究,使数控伺服系统的进给性能,砂轮、导轮的磨削与修整性能,机床加工的稳定性等关键指标得到有效提升。研发达到国际先进水平的高精度数控滚子外圆磨床。通过对引进的高精度滚子外圆数控超精机的技术特点进行深入研究,实现消化吸收再创新,自主研发达到国际先进水平的高精度滚子外圆数控超精机;深入研究滚子修型技术与装备,研发专用超精导辊磨床,在实践中探索提高滚子的使用寿命的有效途径。针对从多个国家引进的多种型式的滚子数控球基面磨床的特点进行深入分析博采众长,把着力点放在自主创新上,研制适合我国国情的,加工精度和加工效率高,性价比好的滚子数控球基面磨床。推广应用应用不漏检、不误判、高效可靠的在线滚子光电外观自动检测和无损探伤装备。将上列自主研发的先进的数控装备进行系统集成,组成具有自动加工手段,自动检测功能,自动反馈模式,自动统计方式,可实现自动清洗、涂油、包装、全线节拍协调一致的滚子磨超自动生产线。通过组建专业化制造联线,进一步稳定产品质量,提高生产效率,将工装、模具进一步标准化,对滚子质量的提高起到推动作用。研发应用达到国际先进水平的、表面应力状态精确可控的滚子表面强化技术和装备。总之,随着轴承行业的高质量发展,将对轴承滚子质量提出了更高的要求。希望通过轴承行业“十四五”的共同努力,使轴承滚子的制造水平跃上一个新的台阶,满足为国家高端装备的配套要求。